Create Your First Project
Start adding your projects to your portfolio. Click on "Manage Projects" to get started
Capstone: Controllable 3D-Printer Extruder for Non-Filament-Based Materials
Project type
Capstone Project
Date
Spring 2023
Location
Notre Dame, IN
For my mechanical engineering senior capstone project at the University of Notre Dame, a team of peers and I were assigned to design, build, and program an extruder for a non-filament-based 3D-printer. For the purposes of demonstration, we were tasked extruding chocolate bark at speeds set by a user in real-time.
The capstone course was constructed to mimic a co-op, wherein my team and I were given a problem with imposed constraints, a budget to accomplish it, and tasked with making weekly presentations to our manager (professor) regarding our progress, and finally to demonstrate a working prototype and justify all engineering design decisions and budget expenditures.
My team chose to create a hopper to contain melting chocolate bark from an oil funnel wrapped with electronic PWM heating elements and controlled by a water-proof thermistor inserted into the mass and wired to an Arduino microcontroller. This hopper fed into an Archimedes-screw/auger within a extrusion enclosure (both of which we and printed from High-Temperature FORMLABS Resin), and extruded chocolate from market-sourced 3D-printer nozzles. The auger was actuated by a stepper motor mounted above it that controlled by a dial potentiometer - the user-determined readings from which were mapped by the Arduino to extrusion speeds. A MATLAB script and GUI collected and displayed information regarding the temperature of the chocolate and the speed of extrusion, to validate the thermal capabilities of the machine as well as its ability to reach a maximum speed and start and stop extruding immediately.
We designed the apparatus over the course of four months, starting with theory from heat transfer, design of machine elements, fluid flow (chocolate being a non-Newtonian fluid), and statics courses to validate design choices for testing. The most difficult part of the project, besides determining how to work within a set of constraints defined explicitly and implicitly by management as well as those the team set for ourselves, was thermal control, as if the chocolate burned in the slightest amount, the crystals would clog the 0.4mm nozzle at the end of the extruder, and the machine would need to be flushed and restarted. At the end of term, the machine performed perfectly, and the extruded flow was consistent and controllable enough to write, in cursive, with the chocolate.

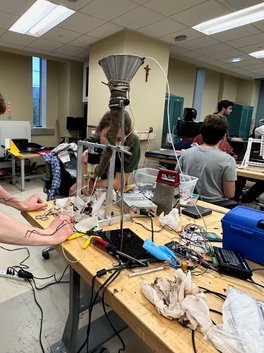



